On This Page
Everything You Need To Know
G10 Machining is used widely to laminate products across industries. This process was created by manufacturers in flat sheets that can be as thin as just a few millimeters. For this reason, it’s used in applications you probably wouldn’t even consider. G10 is used in almost every type of consumer electronic device on the market, especially those with a printed circuit board.
Nowadays, G10 machining is usually referred to as G10-FR4. FR4 machining is short for “flame retardant,” which means that those materials are resistant to fire. This means that G10-FR4 materials can be used in processes like die cutting and machining because they are safe and effective.
G10-FR4 materials have replaced the standard machining materials due to their flame resistant epoxy coating. If you think about electronic products like computers and cell phones, then you know that these devices can heat up fast. Thankfully, the innovation of G10 machining allows for these devices to remain safe, even when they start to heat up.
Utilizing G10 Machining
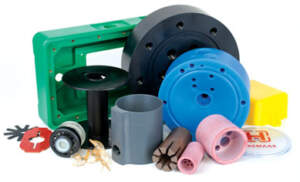
Although G10 machining is a common type of plastic machining service, that doesn’t mean it’s always easy to perform. This type of machining takes special skills in order to create a final product. This material requires custom fabrication, and it’s not an injection molding type of material.
G10-FR4 material is difficult to machine because it requires specialized cutters. That’s because the material itself is strong and durable, which is good for the final application. But, if you’re performing G10 machining at your facility, you likely have expensive cutters to get the job done right. With the right tools, G10-FR4 material can be machined, fabricated, and assembled into a quality final product.
G10 Real World Applications
As mentioned, this process is used in dozens of industries, many of which you probably wouldn’t even consider. G10-FR4 material has little water absorption, and it’s epoxy coating bonds well with other epoxies. In addition, G10 machining is non-corrosive, which is an enormous benefit when it comes to metal processing. This material is great for back plates for high load applications, such as engine mounting brackets.
This process is used often in the boating industry. Particularly, it’s used in the engine room in ships. As mentioned, this material doesn’t absorb water easily, so it’s safe to have it in areas where water exposure is possible. This is combined with the fact that G10-FR4 material is fire resistant. An engine room in a ship will inevitably have oil and moisture, but you can have peace of mind knowing this material won’t cause issues in a potentially flammable area.
G10 machining is also used in the knife making industry. This material is ideal for creating the handles of knives, as well as firearm grips. That’s because these applications require high strength and low absorption to function effectively. Handcrafted applications also usually need to be textured so they can be used easily. This process allows for a high level of precision and texture when creating the final product.
If you are using an electronic switch at work, or typing on your computer, you’re probably reaping the benefits of G10 machining. When it comes to finding the right plastic machining service, the benefits of this material and process can’t be overlooked.
Get Started With G10 Machining Today
Now that you know the benefits of G10 machining and FR4 machining, you can think creatively of ways your industry utilizes this manufacturing process. This may not mean that you want to use G10 machining at your facility, however. Thankfully, there are experts who do everything from G10 machining, to plastic CNC services, to injection molding. Look for reputable plastic processing and G10 machining companies, and talk to them about your needs. Soon you’ll come to understand the importance of G10 machining.